What if we told you that you could speed up curing precast concrete, without the use of any additives, by as much as 300%? If you’re first thought is: prove it, then we would love to. In fact, it may interest you to know that the inception of Powerblanket heating solutions started with concrete curing. We’ve been in the business of increasing concrete curing efficiency for many years, and our solutions have been proven to increase curing efficiency without any of the common side effects related to other forms of acceleration.
CURING PRECAST CONCRETE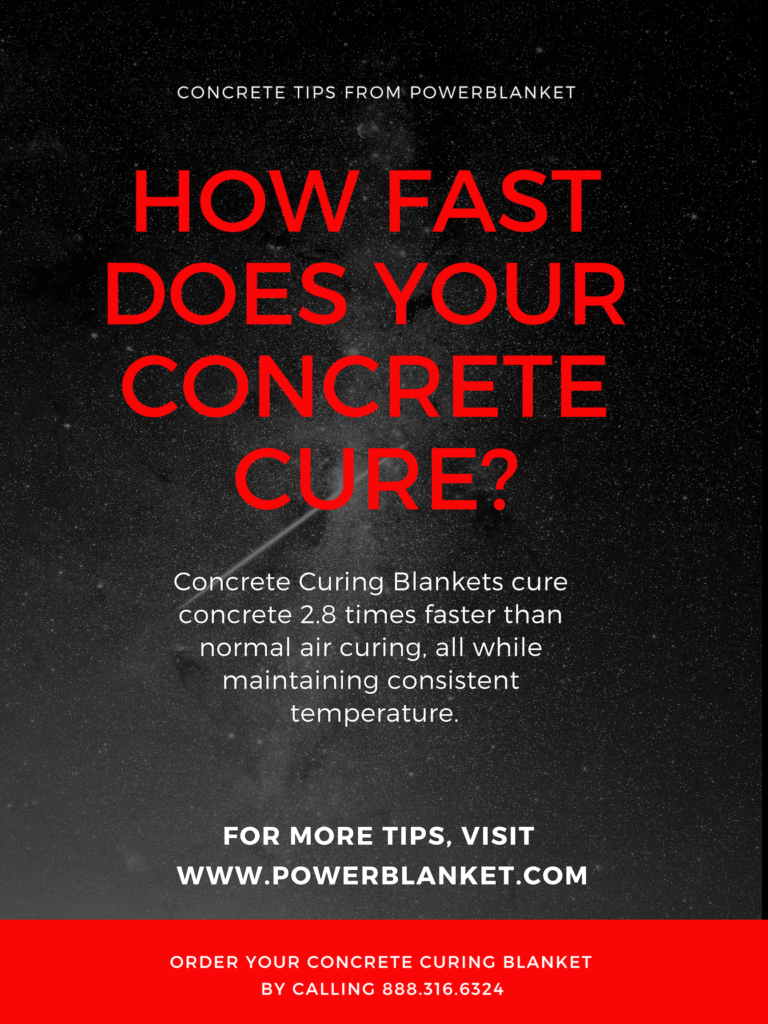
The precast concrete industry, which focuses primarily on custom projects and applications, adheres to strict quality controls for production purposes. These quality controls include paying close attention to the raw materials such as sand, cement, aggregates, chemicals (if needed) and water used in the process and development of the proper mix design. All of these efforts would be rendered meaningless if proper curing procedures and techniques were not followed closely.
COMBATTING COLD TEMPERATURES
Today, there is a higher demand for greater strength in a shorter curing time. While these issues can challenge production at any time, it is particularly challenging when temperatures drop. Â Common problems encountered during the cold-climate times of the year can include but are not necessarily limited to:
- Potential freezing in the early stages of placement
- Inability to achieve required compressive strengths within a specified period of time
- Improper curing procedures
- Frequent and/or rapid temperature change
MOISTURE
One of the more critical elements in the curing process is moisture retention. Moisture evaporation rates need to be controlled, and cold weather is an unacceptable excuse for delaying production. Â Cycle time can obviously take longer during periods of cold weather and we all know that time is money. In situations where the ambient temperature slows both the evaporation rate and thus the curing time, utilizing heat in conjunction with moisture curing has proven to be a successful solution. Using an electrically powered heating blankets which provides even heat distribution reduced the cycle time by as much 33%.
STEAM CURING
Two of the most common and conventional means of providing heat in a precast operation during initial cure are steam and hot air. While effective during the “initial” curing stage, neither method is recommended once the concrete slab has attained its “initial” set. The use of an electrically powered heating solution can provide several benefits:
- Freeze protection
- Sustainability of acceptable temperatures to enhance cure
- Accelerate the achievement of specified compressive strength levels while preventing rapid temperature fluctuations during the curing cycle
Click here to understand the factors that impact precast concrete production and general concrete construction in cold-weather and the standards to which you are looking and needing to adhere to.
ADDITIVES
Additives can dehydrate your concrete and leave you playing a game of gains and losses. Powerblanket custom precast concrete curing solutions keep concrete insulated and hydrated throughout the curing process. Our patented blend of technology allows for the even and consistent curing of precast forms of all shapes and sizes.  Chemical admixtures were used to increase the cure time of concrete before Powerblanket came along to change the game. The problem with chemical additives is that they dehydrate the concrete as they speed up the curing process. And as any concrete expert knows, that’s a big problem.  Rather than balancing the pros and cons of using additives or accelerators in your concrete forms, learn more about concrete curing blankets here.
POWERBLANKET AND CURING PRECAST CONCRETE
Powerblanket started over a decade ago because we wanted to cure concrete faster and more efficiently. The idea for accelerated concrete curing was no new idea.
Powerblanket concrete curing blankets keep moisture in the concrete while producing insulation, protection, and heat—all of which increase curing efficiency by 300%. That’s right, and in the case of pouring concrete into forms, this level of increase makes a real difference. Adding customized Powerblanket heating solutions to your precast concrete business means that you can increase your throughput substantially. If you’re pouring only once a day, adding a Powerblanket solution to your process means you’ll be able to pour three times a day.
And the beauty of Powerblanket heating solutions is that they’re easy to install, remove, transport, and store. So when a form of concrete is cured, you can remove the blanket quicker than the form itself. Additionally, Powerblanket heating solutions can be customized to fit just about anything. So if you use unique precast forms, there’s no need to fret. To put it simply: if you can build it, produce it, or store it, Powerblanket can cover it.
Frequently Asked Questions
How do you cure precast concrete?
Precast concrete is often cured using accelerated methods like steam curing or heated blankets, which enhance strength gain by maintaining consistent temperatures and moisture levels.
Should precast concrete be sealed?
Yes, sealing precast concrete is essential to protect it from weathering, water penetration, and other external influences, thereby prolonging its service life.
Why is precast concrete cured with steam?
Steam curing accelerates the development of compressive strength in precast concrete by increasing the rate of cement hydration through elevated temperatures.
When can I start curing after casting concrete?
Curing should begin immediately after casting to ensure optimal strength and durability, with methods like heated blankets providing effective solutions for maintaining necessary conditions.
Cure your concrete faster and better in cold weather conditions with Powerblanket.